Rotational Molding Machine: Crafting Durable Hollow Plastic Products with Precision and Versatility
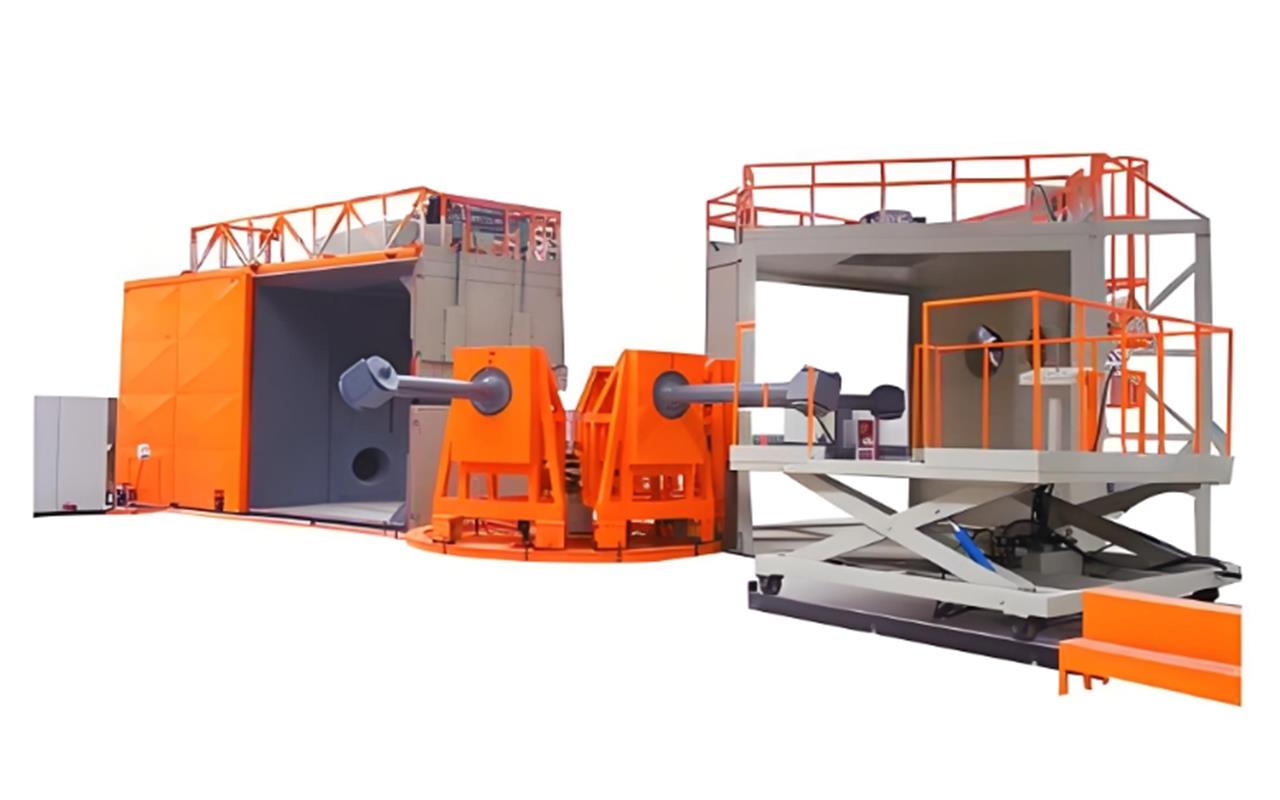
Rotational molding machines (rotomolding) specialize in manufacturing seamless, stress-free hollow plastic products like tanks, containers, and playground equipment. This process is ideal for large, complex shapes that require uniform wall thickness and high durability.
What is a Rotational Molding Machine?
It heats plastic powder (typically polyethylene) inside a rotating mold, allowing the material to coat the mold’s interior through centrifugal force. The result is a lightweight, corrosion-resistant product with no welded joints.
Types of Rotational Molding Machines
- Rock and Roll Machines:
- Rotate molds on two axes (major and minor) for small to medium parts (e.g., kayaks, traffic cones).
- Clamshell Machines:
- Open/close molds vertically for easy loading/unloading. Used for large industrial tanks.
- Carousel Machines:
- Multiple molds rotate through heating, cooling, and loading stations for high-volume production.
- Shuttle Machines:
- Move molds between ovens and cooling chambers, ideal for heavy-duty products.
Key Advantages
- Design Flexibility: Produce complex geometries with undercuts and varying thicknesses.
- Low Tooling Costs: Molds are 30–50% cheaper than injection molding.
- Material Efficiency: Zero waste—excess powder is reused.
Applications
- Agriculture: Chemical storage tanks, irrigation systems.
- Automotive: Fuel tanks, air ducts.
- Recreation: Kayaks, playground slides.
Operation Steps
- Mold Preparation: Load powder into the mold and secure it.
- Heating & Rotation: Heat to 300°C while rotating on two axes for 15–30 minutes.
- Cooling: Gradually cool with air or water sprays.
- Demolding: Open the mold and remove the finished product.
Sustainability Features
- Recycled Material Use: Up to 100% post-consumer polyethylene.
- Energy Recovery: Capture oven heat for preheating molds.